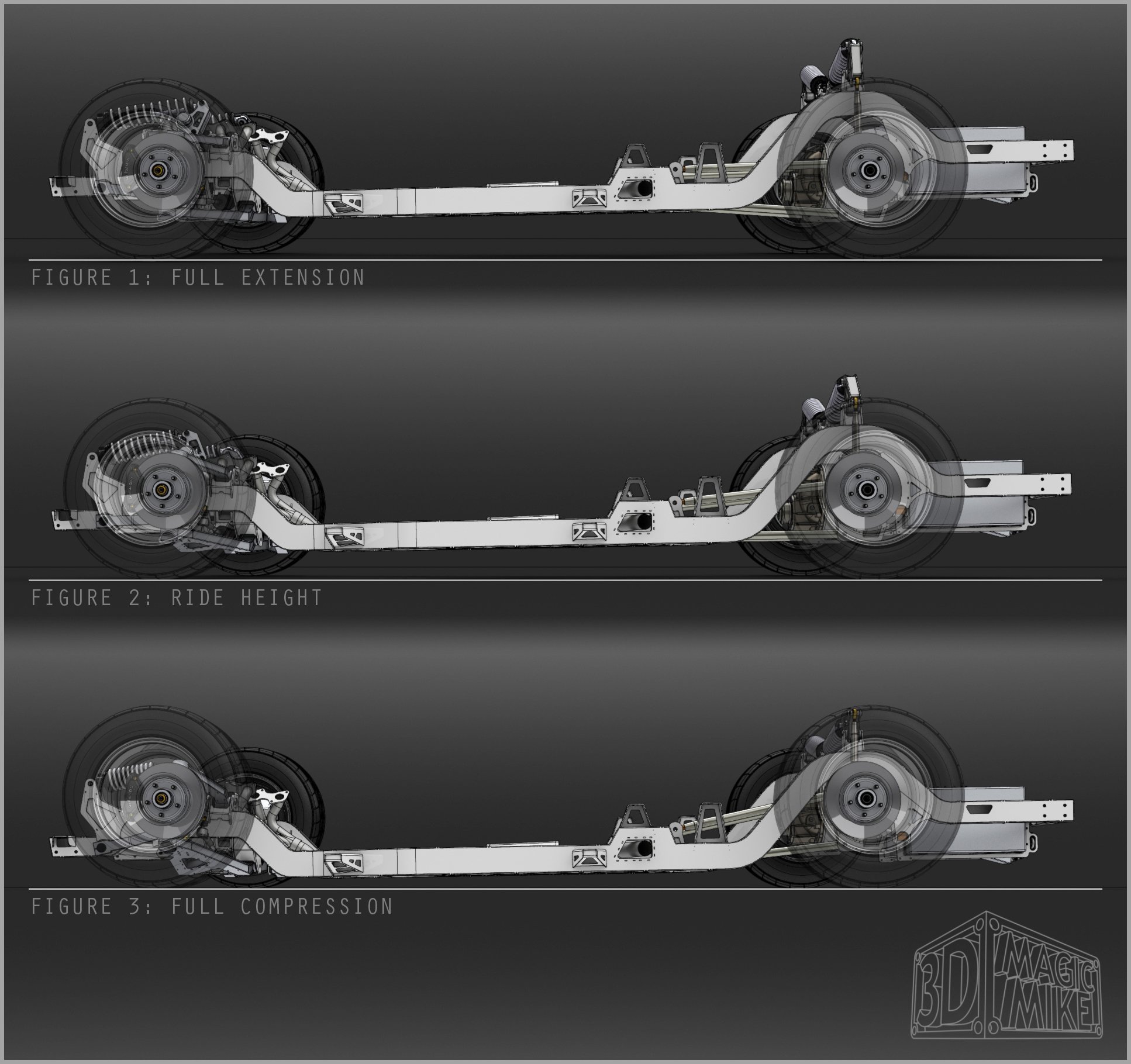
Datsun 620 custom chassis
The Datsun 620 build all started around a completely new, ground up bespoke chassis design that would define the rest of the build. With a focus on cantilever front and rear suspension, an SLA independent front suspension with idealized geometry, and wide and aggressive track width with an intent to flare the truck, the chassis would define many of the building points of the project and how it would ultimately come together as a whole. This chassis had gone through quite a few changes over its lifespan as the project evolved, originally being a budget N/A rat rod build and slowly snowballing into the rear mounted twin turbo system it is today.
The chassis design started with simple hand-measurements, as this chassis design pre-dated any access or experience with 3D-scanners for this type of design work. People always assume that a 3D scanner is the only way to design a system as complicated as a full chassis, but that couldn’t be farther from the truth. Simple and thoughtful hand measurements can really tell the entire story as long as the process is done correctly. Using nothing more than tape measures, plumb bobs, long levels and some tape and sharpies, the entire original chassis and body/bed references were hand measured to central datum points and recorded on paper. From that data, the basic plot points of the chassis were transferred to the computer and the design started.
Lots of design elements were brought into the chassis right off the bat, mostly being driven by the components used on he build. The front sump 1UZFE engine required the use of a rear steer IFS rack system, the larger wheels and tires forced me to lengthen the wheelbase and push the wheels away from their original centerlines, and much more. Taking as many design elements into consideration while the chassis was evolving, the final product created an an amazing baseline for the build to start around.
Chassis fabrication was helped in a big way by my good friend and experienced chassis builder Mike Schmidt, who helped to jig the chassis and true it from its separate components. While I TIG welded most all the small sub assembly structures from mild steel, Schmidt welded those part sets into the master chassis while it was in the jig. Working in tandem, the entire chassis was welded out and eventually made its way out of the jigs and onto the floor for assembly.
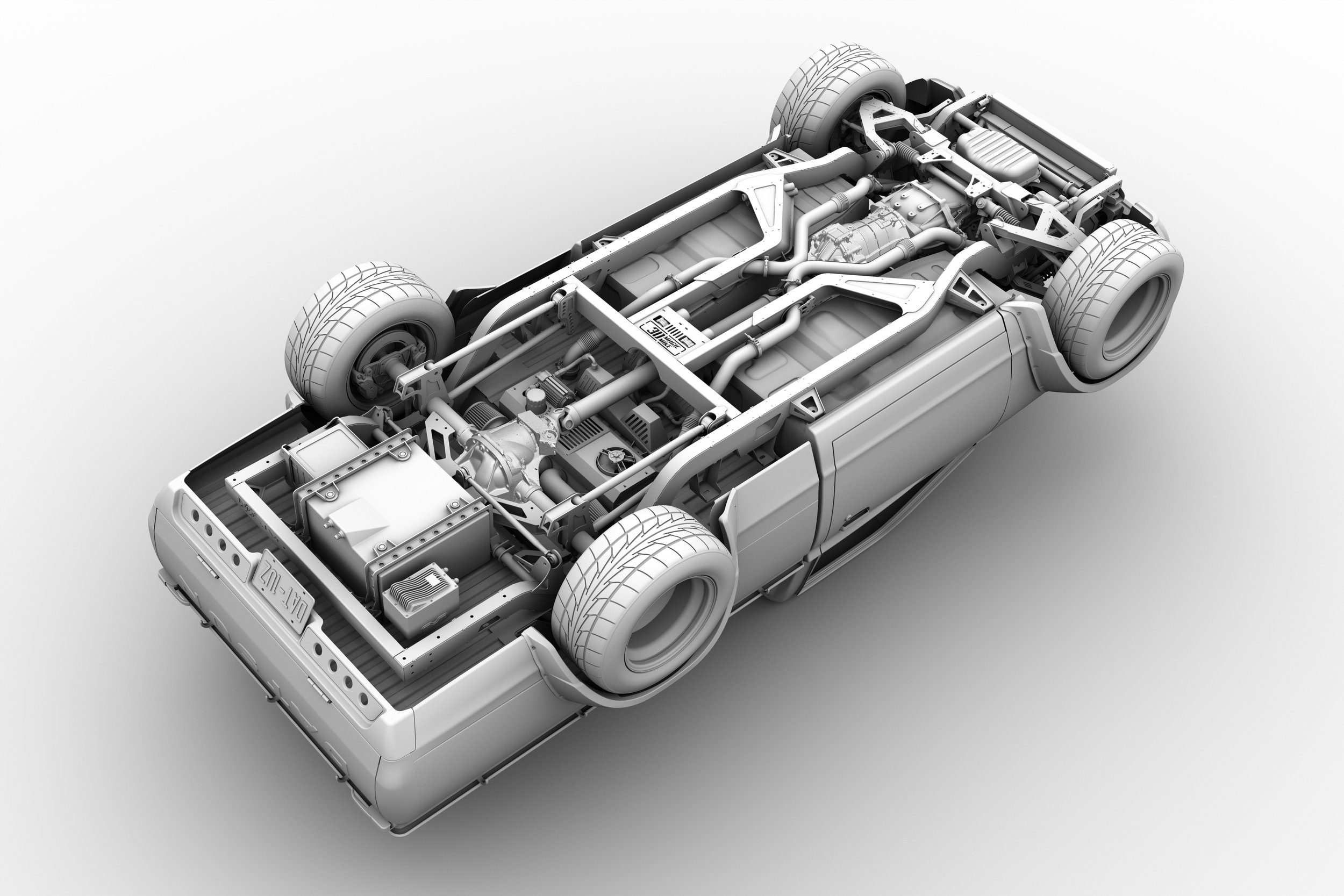
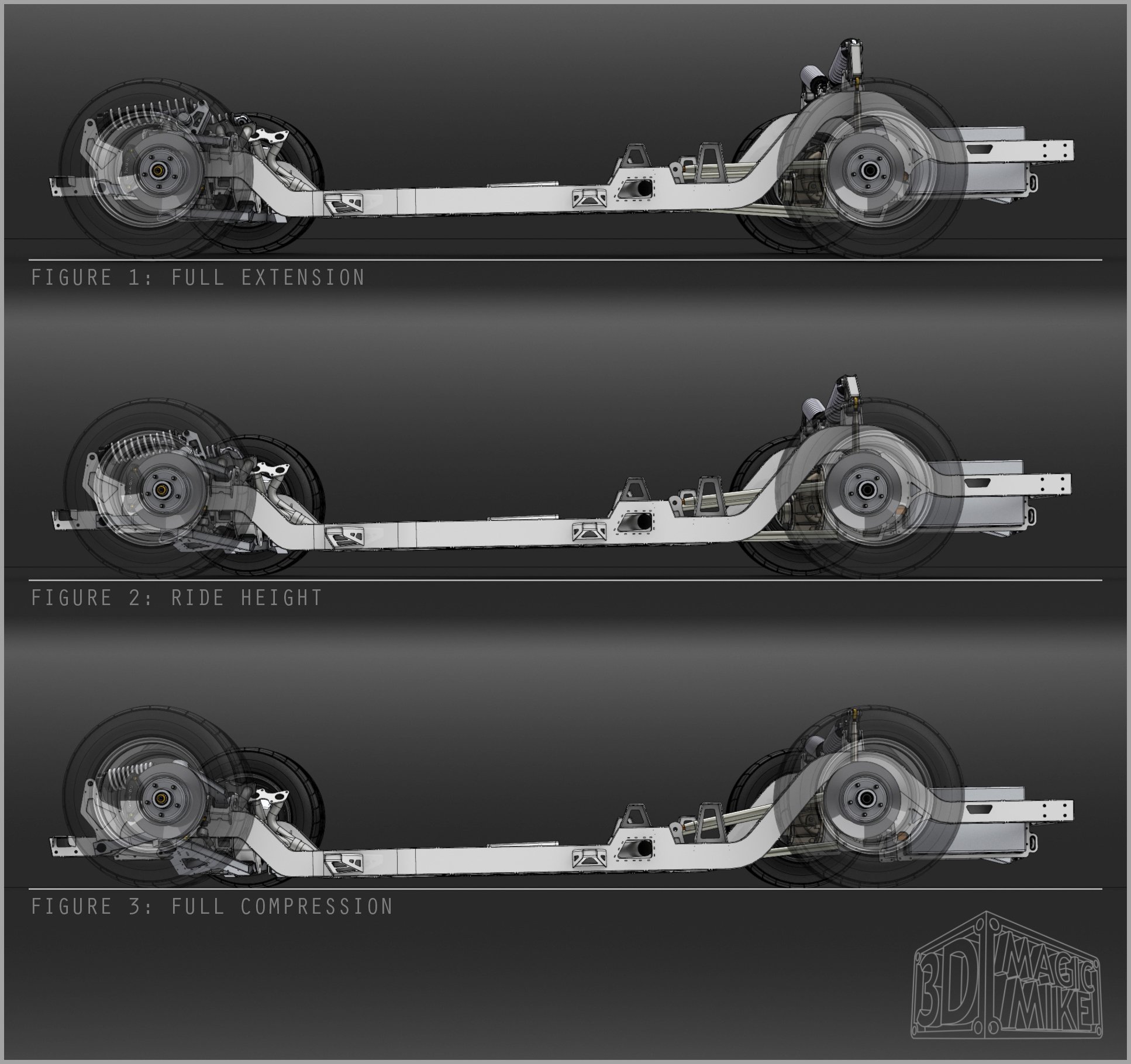
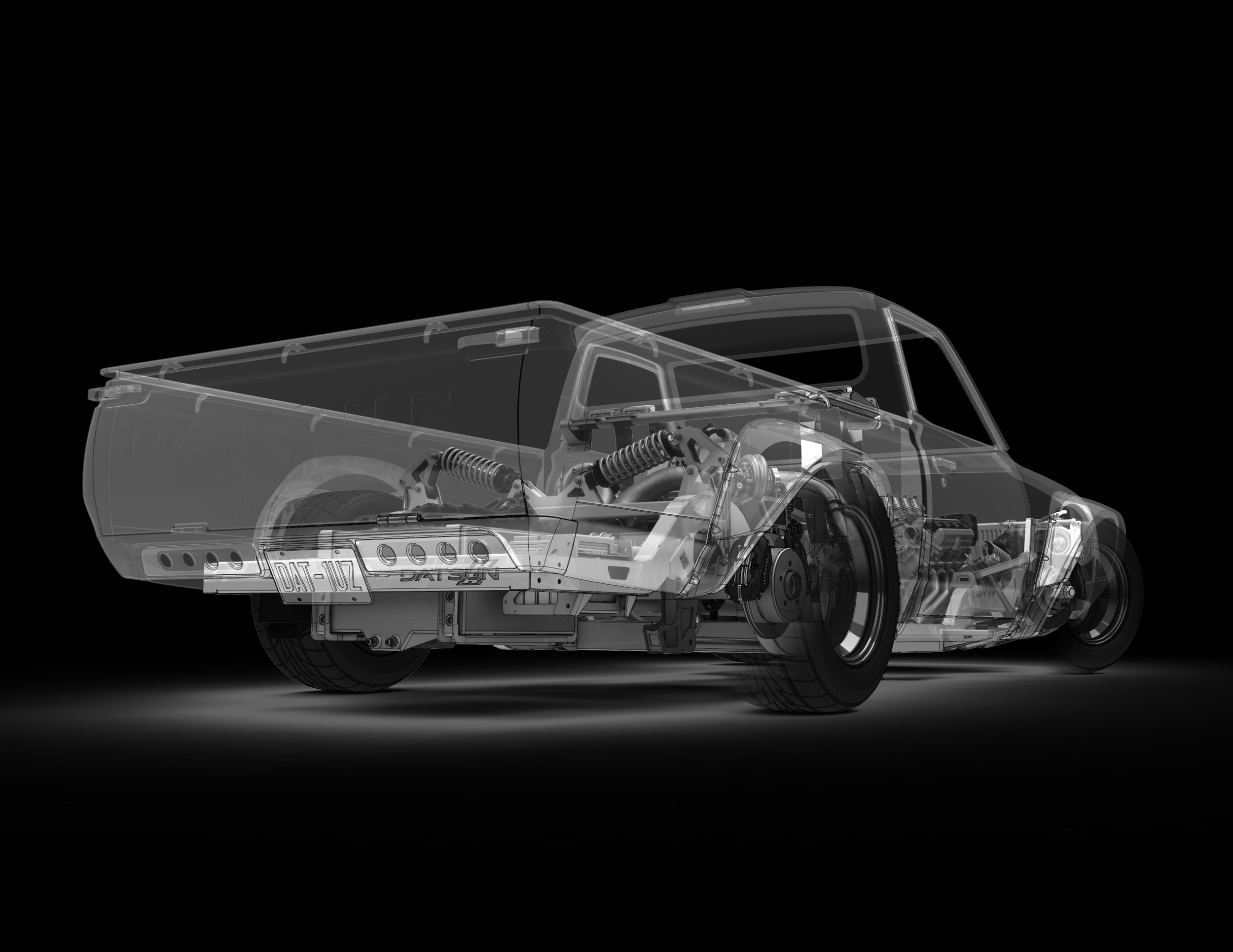
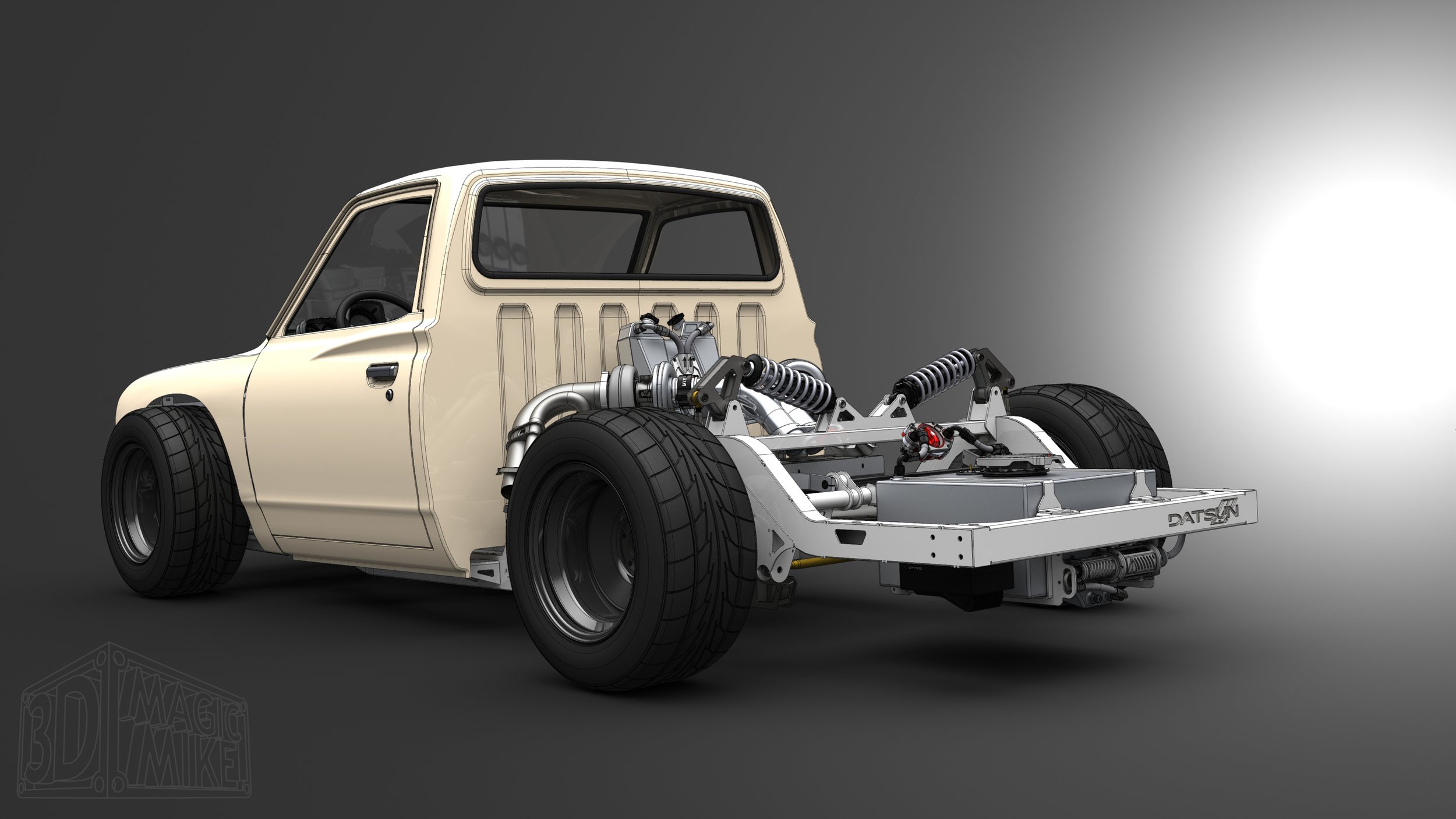